Snapmaker Doppelextrusion 3D-Druckmodul (inkl. MwSt.)
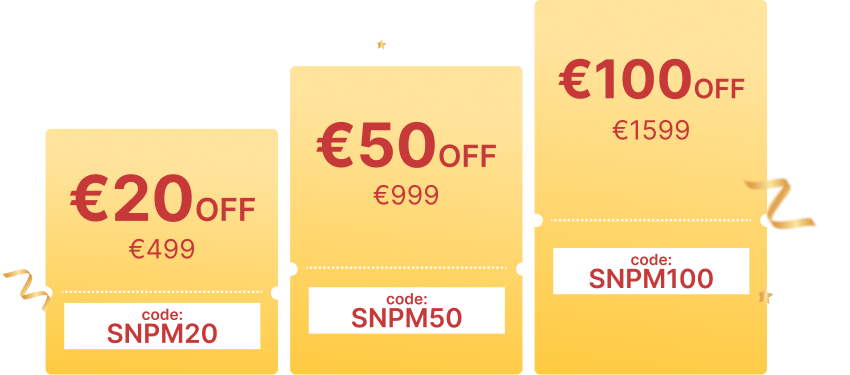
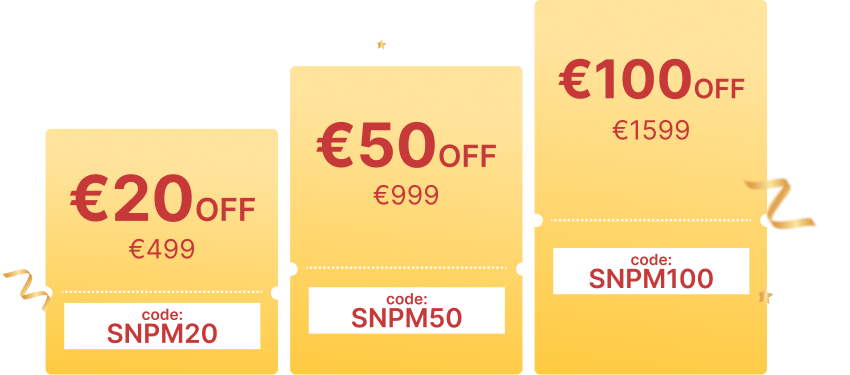
Allgemeine Merkmale:
• 3s-Schalter für Heizblock
• 300 °C Doppelextrusion
• Lösliche und abbrechbare Supports
• Fortschrittlicher Materialdruck
• 4-Lüfter-Kühlsystem
• Kompatibilität mit verschiedenen Düsengrößen
• Automatische Nivellierung
• Intelligente Auftragswiederherstellung
Kompatibilität:
• Snapmaker 2.0 A350T/A350/F350
• Snapmaker 2.0 A250T/A250/F250
• Snapmaker 2.0 A150
* 2 Heizblöcke mit 0,4 mm Messingdüsen sind im Lieferumfang enthalten.
Zwei Jahre Garantie inbegriffen. Inkl. MwSt.
4+ rolls at €19.99/roll, 8+ rolls at just €18.99/roll
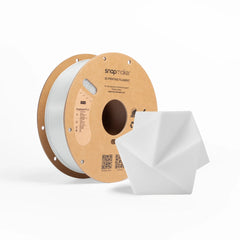
SnapSpeed PLA Filament (1kg)
€22,90 €26,99
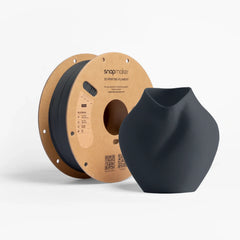
Matte PLA Filament (1kg)
€22,90 €23,99
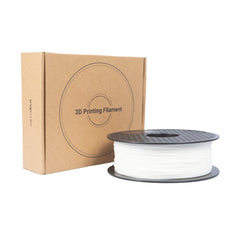
PLA-Filament (1 kg)
€22,90 €28,99
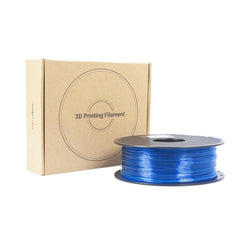
PETG-Filament (1 kg)
€22,90 €28,99

ABS-Filament (1kg)
€22,90 €28,99
Verfügbarkeit für Abholungen konnte nicht geladen werden
Payment methods
Earn [points_amount] when you buy this item.
Snapmaker
Materials Printing
Cooling System
Levelling
Breakaway Supports
10+ Combo of Materials
Dual extrusion is an acquired taste, one you will stick to once learned, because there are some things in 3D printing that a single hot end just doesn't quite cut it. A sophisticated print with fine details. A gadget that combines PLA and TPU. A dual color little thing that your kid has been dying to have.
PVA
Breakaway Support for PLA
We all know what a pain removing support materials can be. Don't let it ruin your fun. Throw in a spool of water soluble PVA filament and watch your print emerge from water like the beauty it's meant to be. You can do the same with HIPS and breakaway support, with a little help of oil or none.
Multi-color Printing
Quick-swap Hot Ends
All the Gears and Ideas
What about print quality, you might ask. Let's first add this up: stepper motor + planetary gear + dual extrusion gears for each hot end = ?
The 7.5:1 planetary gears transmit power from the motor with much greater torque, which allows us to use relatively small motors to achieve needed pulling force. Shedding unnecessary weight will in turn results in a much smaller vibration of the toolhead at the same rate of acceleration, thus keeping the same printing precision as the single extrusion module.
Single Extrusion Module
Dual Extrusion Module
Meanwhile, the 68-teeth gears with a 12 mm diameter allow for sufficient contact surfaces with the filament they are pulling in, applying steady force so your filament won't come out of the nozzle all beaten up. So back to the question: what's the other end of the equation? The answer is flawless extrusion with 20 mm³/s flow rate and high quality results.
Wanna Print Non-stop? Keep It Cool.
Now the second pain other than removing support, has to be picking filament debris out from a jammed nozzle. Well, hopefully you won't have to deal with it for a long time with Dual Extrusion Module.
Each of your hot end has a dedicated fan blowing much needed wind from a blower, preventing your filament from melting prematurely in the heat sink which invariably ends up clogging the hot end.
Also, if you are still caught up on that time when your overhang failed miserably on you, worry no more, because your overhangs will be cool this time. Another set of fans are located at the bottom right and left. They will keep your nozzles and prints cool. So whether you are printing a bold overhang, or with ABS/PA, dive in head first; you can adjust the fan speed later[2].
Great Hot Ends Work Async
Get Smart with Various Nozzle Sizes[1]
To make smarter use of nozzles, you can tune your settings a bit more with each nozzle size in Luban. When you want a print with impeccable details, print the shell at a lower speed with the 0.2 mm-nozzle hot end, so it's not only sturdy but looks fine on the outside. And when you want speed for a model that's rich in support structure, print the infill with 0.6 or 0.8 mm-nozzle hot end, because they are way quicker.
Auto Levelling
Power-loss and Filament Run-out Recovery
Specifications
Dimensions (W × D × H)
108 mm × 70 mm × 133 mm
Package Dimensions (W × D × H)
279 mm × 254 mm × 177 mm
Frame Material
Aluminum alloy
Weight
1.0 kg
Package Weight
3.2 kg
A150 Work Area
145 mm × 145 mm × 105 mm
A250/A250T/F250 Work Area
230 mm × 240 mm × 190 mm
A250T(Quick Swap) Work Area
230 mm × 225 mm × 175 mm
A350/A350T/F350 Work Area
320 mm × 330 mm × 285 mm
A350T(Quick Swap) Work Area
320 mm × 315 mm × 270 mm
Flow
20 mm³/s
Nozzle Diameter (Standard)
0.4 mm
Nozzle Diameter (Optional)
0.2 mm, 0.6 mm, 0.8 mm
Nozzle Material (Standard)
Brass
Nozzle Material (Optional)
Hardened steel
Max. Nozzle Temperature
300°C
Max. Recommended Printing Speed
100 mm/s
Supported Materials[3]
PLA, ABS, ASA, PETG, TPU (Hardness ≥ 90 Shore A), Breakaway Support for PLA, PVA, HIPS, Nylon, Carbon Fiber Reinforced Nylon, Glass Fiber Reinforced Nylon
Supplied Software
Snapmaker Luban (Third-party software supported)
Input Voltage
24V DC
Operating Temperature
15°C–30°C
Supported File Formats
stl, obj
In the Box
Dual Extrusion 3D Printing Module × 1
Quick Start Guide × 1
Filament Holder Sheet × 1
Filament Holder Cap × 1
Filament Holder Tube × 1
Filament Tube × 2
Filament Tube Fixture × 1
Wiping Cloth × 1
Calibration Card × 1
Cable Clip × 2
Wire Brush × 1
M4 x 10 Hex Socket Head Screw × 5
T Nut × 1
Stainless Steel Stud Bolt × 1
M4 × 12 Hex Socket Head Screw × 4
[2] Note that without the Snapmaker Enclosure, the noise level when you put all fans at full speed, will be 55.6 dB; while with Snapmaker Enclosure, the noise level will be 42.3 dB.
[3] Hardened steel nozzle should be used when printing with nylon and reinforced nylon filaments.
Frequently Asked Questions
1. Is the hot end from the Single Extrusion Module compatible with the Dual Extrusion Module?
No, the hot ends are not compatible. The Dual Extrusion Module has a quick-swap hot end for easy installation and replacement.
2. Can the Snapmaker 2.0 Dual Extrusion Module print food-safe materials?
Yes, it can print with food-safe materials like PLA. Ensure the entire filament path, including the nozzle and extruder, is clean and uncontaminated for food safety.
3. Can I print with two colors using the Snapmaker 2.0 Dual Extrusion Module?
Yes, the dual extrusion module allows dual-color prints by switching between filaments during a single print.
4. Does the Snapmaker 2.0 Dual Extrusion Module require any special maintenance?
It is easy to maintain. Regularly includes:
●Clean the nozzles to prevent clogs
●Check for debris around the extruders
●Checking cooling fans to ensure proper airflow during prints
Keeping these parts clean ensures optimal performance and better print quality.
5. What are the differences between the J1s IDEX 3D Printer and the Dual Extrusion 3D Printing Module?
The J1s IDEX 3D Printer features independent dual extruders, allowing simultaneous prints on two objects. In contrast, the Snapmaker 2.0 Dual Extrusion Module has two extruders integrated into one module, sharing a single X-axis, limiting it to printing with two heads on the same object.
6. What are the key upgrades of the Snapmaker 2.0 Dual Extrusion Module over the Single Extrusion Module?
●Cooling: Dual has 4 fans, Single has 2.
●Extrusion Flow: Dual supports 20 mm³/s, Single 9 mm³/s.
●Calibration: Dual supports XY offset calibration.
●Extruder Switching: Dual uses motorized lifts.
●Hot End: Dual has quick-swap hot ends.
●Materials: Dual supports more filaments, including PVA and TPU.
●Max Temp: Dual reaches 300°C, Single 275°C.
The Dual Extrusion Module offers faster, more versatile printing with better material compatibility for complex projects.
7. How does the auto-leveling function work with the Dual Extrusion Module?
It uses a proximity sensor to measure multiple points on the heated bed, automatically adjusting for any unevenness. This ensures both nozzles are precisely aligned without the need for manual calibration. Additionally, the optoelectronic switch handles Z-height calibration, making setup smooth and hassle-free.
8. How can the Snapmaker 2.0 Dual Extrusion Module improve print precision?
The 7.5:1 planetary gears generate higher torque, reducing toolhead vibration for smooth, stable, and precise prints, even at higher speeds.
3D Printing Module
Materials Printing
Cooling System
Levelling
Keep It Cool.
So the classy and efficient way to do it, we decided, is to switch with a motor. When your g-code tells the motor it's time to change the hot end, the motor will ask the linear rail to do the heavy lifting. Then the hot end gets changed, and the printing continues. This is done within 3 seconds, with a repeatability of 0.012 mm.
Nozzle Sizes
Dimensions (W × D × H)
108 mm × 70 mm × 133 mm
Package Dimensions (W × D × H)
279 mm × 254 mm × 177 mm
Frame Material
Aluminum alloy
Weight
1.0 kg
Package Weight
3.2 kg
A150 Work Area
145 mm × 145 mm × 105 mm
A250/A250T/F250
Work Area
230 mm × 240 mm × 190 mm
A250T(Quick Swap)
Work Area
230 mm × 225 mm × 175 mm
A350/A350T/F350
Work Area
320 mm × 330 mm × 285 mm
A350T(Quick Swap)
Work Area
320 mm × 315 mm × 270 mm
Flow
20 mm³/s
Nozzle Diameter (Standard)
0.4 mm
Nozzle Diameter (Optional)
0.2 mm, 0.6 mm, 0.8 mm
Nozzle Material (Standard)
Brass
Nozzle Material (Optional)
Hardened steel
Max. Nozzle Temperature
300°C
Max. Recommended
Printing Speed
100 mm/s
Supported Materials[3]
PLA, ABS, ASA, PETG, TPU (Hardness ≥ 90 Shore A), Breakaway PLA, PVA, HIPS, Nylon, Carbon Fiber Reinforced Nylon, Glass Fiber Reinforced Nylon
Supplied Software
Snapmaker Luban
(Third-party software supported)
Input Voltage
24V DC
Operating Temperature
15°C–30°C
Supported File Formats
stl, obj
Dual Extrusion 3D Printing Module × 1
Quick Start Guide × 1
Filament Holder Sheet × 1
Filament Holder Cap × 1
Filament Holder Tube × 1
Filament Tube Fixture × 2
Filament Tubet × 1
Wiping Cloth × 1
Calibration Card × 1
Cable Clip × 2
Wire Brush × 1
T Nut × 1
M4 x 10 Hex Socket Head Screw × 5
Stainless Steel Stud Bolt × 1
M4 × 12 Hex Socket Head Screw × 4
[2] Note that without the Snapmaker Enclosure, the noise level when you put all fans at full speed, will be 55.6 dB; while with Snapmaker Enclosure, the noise level will be 42.3 dB.
[3] Hardened steel nozzle should be used when printing with nylon and reinforced nylon filaments.
Frequently Asked Questions
1. Is the hot end from the Single Extrusion Module compatible with the Dual Extrusion Module?
No, the hot ends are not compatible. The Dual Extrusion Module has a quick-swap hot end for easy installation and replacement.
2. Can the Snapmaker 2.0 Dual Extrusion Module print food-safe materials?
Yes, it can print with food-safe materials like PLA. Ensure the entire filament path, including the nozzle and extruder, is clean and uncontaminated for food safety.
3. Can I print with two colors using the Snapmaker 2.0 Dual Extrusion Module?
Yes, the dual extrusion module allows dual-color prints by switching between filaments during a single print.
4. Does the Snapmaker 2.0 Dual Extrusion Module require any special maintenance?
It is easy to maintain. Regularly includes:
●Clean the nozzles to prevent clogs
●Check for debris around the extruders
●Checking cooling fans to ensure proper airflow during prints
Keeping these parts clean ensures optimal performance and better print quality.
5. What are the differences between the J1s IDEX 3D Printer and the Dual Extrusion 3D Printing Module?
The J1s IDEX 3D Printer features independent dual extruders, allowing simultaneous prints on two objects. In contrast, the Snapmaker 2.0 Dual Extrusion Module has two extruders integrated into one module, sharing a single X-axis, limiting it to printing with two heads on the same object.
6. What are the key upgrades of the Snapmaker 2.0 Dual Extrusion Module over the Single Extrusion Module?
●Cooling: Dual has 4 fans, Single has 2.
●Extrusion Flow: Dual supports 20 mm³/s, Single 9 mm³/s.
●Calibration: Dual supports XY offset calibration.
●Extruder Switching: Dual uses motorized lifts.
●Hot End: Dual has quick-swap hot ends.
●Materials: Dual supports more filaments, including PVA and TPU.
●Max Temp: Dual reaches 300°C, Single 275°C.
The Dual Extrusion Module offers faster, more versatile printing with better material compatibility for complex projects.
7. How does the auto-leveling function work with the Dual Extrusion Module?
It uses a proximity sensor to measure multiple points on the heated bed, automatically adjusting for any unevenness. This ensures both nozzles are precisely aligned without the need for manual calibration. Additionally, the optoelectronic switch handles Z-height calibration, making setup smooth and hassle-free.
8. How can the Snapmaker 2.0 Dual Extrusion Module improve print precision?
The 7.5:1 planetary gears generate higher torque, reducing toolhead vibration for smooth, stable, and precise prints, even at higher speeds.